Crotched Mountain On-Site Wastewater Solution – Greenfield, New Hampshire
The Crotched Mountain Foundation and Rehabilitation Center recently completed the installation of a 100,000 gallon per day, Amphidrome® onsite wastewater treatment system utilizing a blend of advanced wastewater treatment processes.
Crotched Mountain Foundation is a nonprofit charitable organization serving children and adults with disabilities and their families from across the Northeast since 1953. The facility is located on a 1,400-acre campus that includes a residential school for children with special needs, a hospital that focuses on rehabilitation following brain injuries and other neurological conditions, an outpatient clinic, and residential services for adults. The existing wastewater collection and treatment system has suffered from the ravages of time.
The gravity collection system which covers the campus grounds experienced a great deal of (I/I) Inflow and Infiltration. CMRC commissioned Underwood Engineers, Inc., Portsmouth, NH to provide a complete study of the system and design plans for remediation. This work had to be completed prior to the construction of a new wastewater treatment facility.
The existing on-site septic system and leaching trenches also suffered from aging and overloading from the inflow and infiltration. Locating a new site for wastewater discharge presented additional challenges. Due to the mountainous terrain and soil conditions, a fairly large area was required. The available land was also adjacent to sensitive environments, thus dictating the need for a high level of wastewater treatment.
Unique Solutions Required
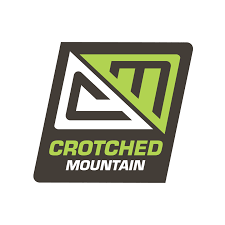
A combination of solutions was found to fit this site. Discharge of treated effluent was handled with a blend of conventional sub-surface trenches and a relatively new process using a sub-surface drip dispersal system. The drip dispersal system, sometimes used as an irrigation device, works with pressure-regulated emitters and provides even distribution of effluent. This provides greater flexibility to permit the use on sloping land.
Advanced Treatment Required
The sub-surface solutions selected still required a great deal of land area. The utilization of an advanced treatment system was found to provide the benefits of higher quality effluent thus permitting a 50% reduction in the sub-surface systems.
CMRC and Underwood Engineers, Inc. selected the Amphidrome Treatment Process due to the experience, performance history, and capabilities to treat the large wastewater flows from this facility. The system was sized to treat and discharge flows up to 85,000 gpd with a potential build out flow to 100,000 gpd.
On July 25th, 2008 CMRC solicited bids for construction of this $3.024M project which was funded through a bond issue, grants from CDBG and USEPA, and a loan from the NH SRF program. The treatment system is now meeting discharge permit limits within the first month of operation.
Project Scope
Contract #1
This contract included the main treatment plant site with a base bid for the 85,000 gpd plant with an alternate to increase the plant to 100,000 gpd.
The contract was awarded to Weston & Sampson, CMR.
Contract #2
This contract included the onsite disposal system and other site improvements to the campus. The contract was awarded to S.U.R. Construction West.
These contractors teamed to provide services to each other under both contracts. The treatment plant went online July 30, 2009. The drip dispersal and trench system followed on September 1, 2009.
The Amphidrome System
The Amphidrome system utilizes two tanks and one submerged attached growth bioreactor, subsequently called Amphidrome reactor.
The first tank, the anoxic/equalization tank, is where the raw wastewater enters the system. The tank has an equalization section, a settling zone, and a sludge storage section. It serves as a primary clarifier before the Amphidrome reactor.
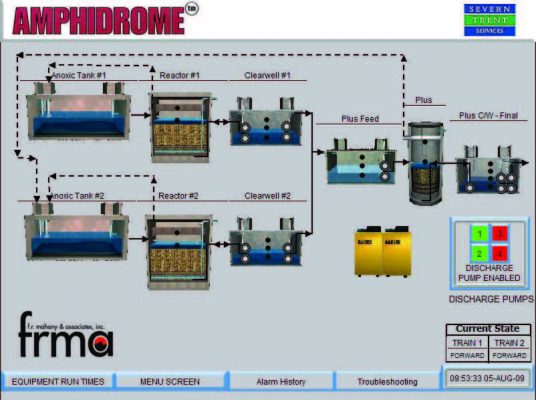
This Amphidrome reactor consists of the following four items: underdrain, support gravel, filter media, and backwash trough. The underdrain, constructed of stainless steel, or HDPE encased concrete block, is located at the bottom of the reactor. The underdrain provides support for the media and even distribution of air and water into the reactor.
Air laterals are provided to distribute the air evenly over the entire filter bottom. The design allows for both the air and water to be delivered simultaneously, or separately via individual pathways to the bottom of the reactor.
The system utilizes an automated PLC control system with touch screen interface to provide the operator easy access to process controls. This system is in use throughout the United States and Poland and has been in use since 1996.
The Amphidrome Process
The Amphidrome system is a submerged attached growth bioreactor process (SAGB) operating in a batch mode. It is a deep-bed sand filter designed for the simultaneous removal of soluble organic matter, nitrogen and suspended solids within a single reactor.
However, if stringent total nitrogen limits, (i.e. less than 10 mg/l), are required, a second smaller polishing reactor is required. Since the process removes nitrogen, it is also classified as a biological nutrient removal (BNR) process.
To achieve simultaneous oxidation of soluble material, and to provide nitrification and denitrification in a single reactor, the process must provide aerobic and anoxic environments for the two different populations of microorganisms.
The Amphidrome process can be used as a stand-alone treatment process or can be used with other processes to provide further treatment. Depending on the discharge permit requirements these systems can include micro-filtration, Chemical coagulation processes and ultraviolet disinfection.
As the air flows up through the media, the bubbles are sheared by the sand– producing finer bubbles as they rise through the filter. On top of the underdrain is 18”, (five layers), of four different sizes of gravel. Above the gravel is a deep bed of coarse, round, silica sand media. The media functions as a filter, significantly reducing suspended solids, and provides the surface area for which an attached growth biomass can be maintained.
To achieve the two different environments required for the simultaneous removal of soluble organics and nitrogen, aeration of the reactor is intermittent, rather than continuous.
Depending on the strength and the volume of the wastewater, a typical aeration scheme may be three to five minutes of air and ten to fifteen minutes without air. Concurrently, return cycles are scheduled every hour, regardless of the aeration sequence. During a return, water from the clear well is pumped back up through the filter and overflows into the trough. The trough is set at a fixed height above both the media and the influent line; and the flow is by gravity back to the front of the anoxic/equalization tank.
The cyclical forward and reverse flow of the waste stream and the intermittent aeration of the filter achieves the required hydraulic retention time and creates the necessary aerobic and anoxic conditions to maintain the required level of treatment.
Applications
The Amphidrome process is used in applications from single-family homes to very large flows in excess of 200,000 gpd.
Applications can include new home construction, remedial applications to fit in reduced space limitations, commercial and residential development and community wastewater treatment solutions.
Effluent quality provides advanced treatment to enable a vast range of discharge solutions from direct soil absorption systems to end of pipe water re-use systems.
Vital Statistics
NH DES Discharge Limits
- Flow 85,000 gpd
- BOD, TSS <30 mg/l
- TN <20 mg/l , <10 mg/l at monitoring wells
Treatment Plant
Dual Train Amphidrome ® Plus 100,000 gpd
- (2) sets of Anoxic tanks in series @ 50,000 per train
- (2) 9.5 by 15 ft. Amphidrome Reactors
- (2) 35,000 gallon clear wells
- (1) Plus Reactor Pump chamber 10 by 52 ft.
- (1) 8ft. Diameter Plus® Reactor
- (1) 10ft. Diameter Final discharge Pump chamber
Structures include:
- (1) Headworks Facility
- (1) Control Building
SSDS
Drip system 48,000 gpd
- (6) Zones @ 67,000 ft.
- (1) Control Building
Trench System 38,400 gpd
- (4) Zones @ 1200 ft.
Collection System
10,850 feet of gravity sewer with a mix of 6, 8 and 10 pipe consisting of PVC, AC and Concrete pipe. Much of this system has undergone rehabilitation including slip lining, pipeline replacement and manhole rehabilitation.